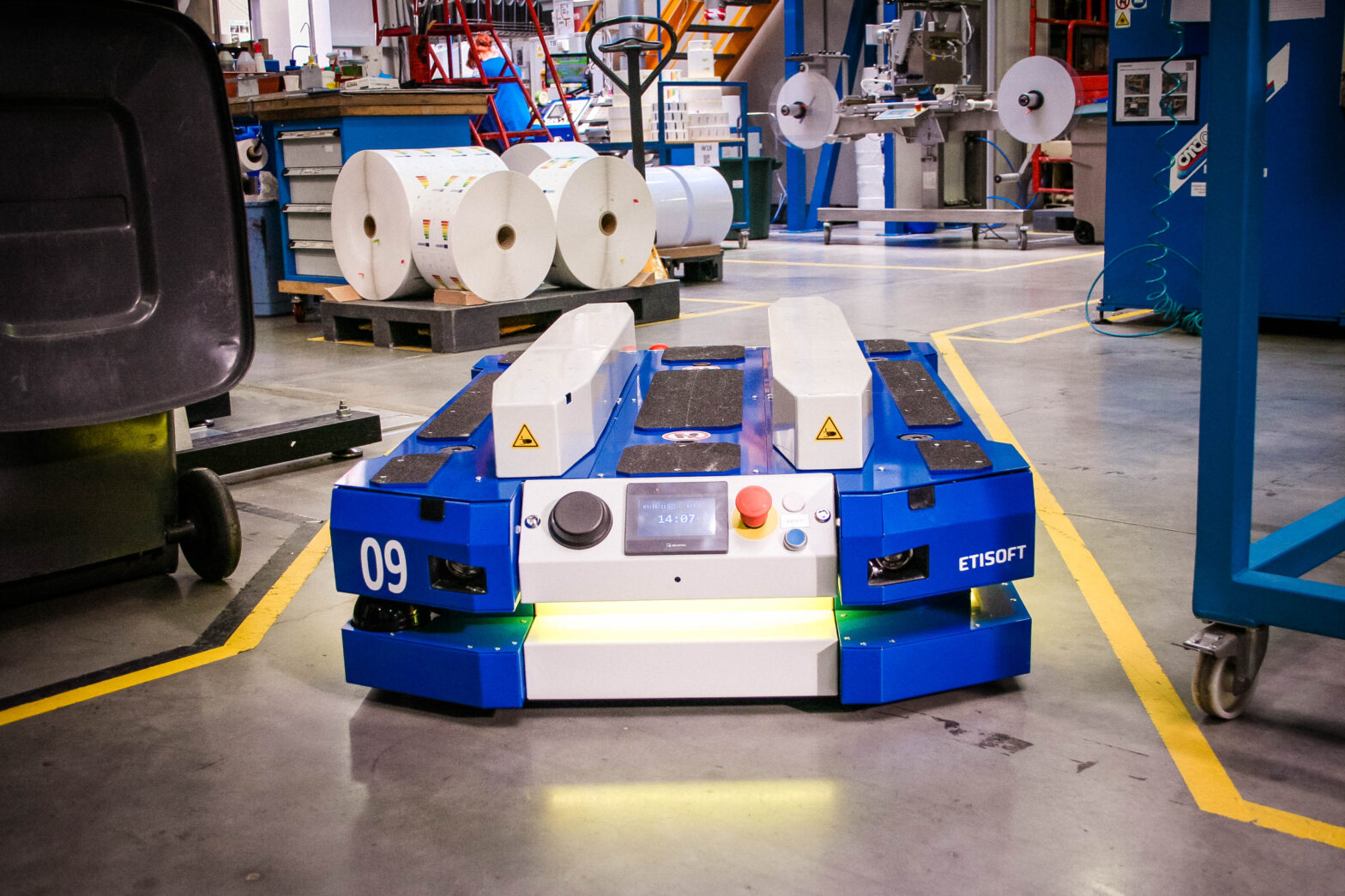
Wdrożenie systemu intralogistycznego z wykorzystaniem robota AGV w zakładzie produkcyjnym etykiet Etisoft Sp. z.o.o
Wdrożenie systemu intralogistycznego miało miejsce w spółce Etisoft na przełomie roku 2020/2021. Zaprojektowaliśmy, zintegrowaliśmy i wdrożyliśmy kompletny system intralogistyczny oparty o robota AGV.
Etisoft jest liderem w swojej branży. Rozwiązanie jakie wdrożyliśmy pokazuje możliwości automatyzacji procesów logistycznych, nawet w zakładach produkcyjnych i magazynach o ograniczonej przestrzeni i uczęszczanych ścieżkach transportowych.
Robot AGV: optymalizacja i automatyzacja procesów logistycznych
Celem projektu była optymalizacja i automatyzacja procesów logistycznych realizowanych przez pracowników działu logistyki wewnątrzzakładowej. System odciąża pracowników podczas czasochłonnych i powtarzalnych czynności. W trakcie realizacji projektu dużym wyzwaniem, z jakim musieli się zmierzyć nasi inżynierowie, była mała ilość miejsca między stanowiskami produkcyjnymi oraz zatłoczone ścieżki transportowe. Implementacja systemu obejmowała:
- robota AGV,
- doki odkładcze,
- ekran pokazujący lokalizację robota i parametry jego pracy,
- system informowanie o stanie doków z wykorzystaniem sygnalizatorów typu „andon”,
- system IntraFleet – zarządzający pracą robota, zleceniami transportowymi zintegrowanymi z systemem MES do zarządzania produkcją.
Wdrożenie systemu intralogistycznego dało naszym klientom możliwość realizacji wizyt referencyjnych oraz przekonania się o możliwościach systemów intralogistycznego i zaletach, jakie płyną z autorskiego rozwiązania spółki córki Etisoft Smart Solutions Sp. z.o.o.
Funkcjonowanie zakładu przed automatyzacją
Przed wdrożeniem projektu magazynierzy obsługiwali stanowiska maszyn fleksograficznych za pomocą ręcznych wózków paletowych oraz pchanych wózków stołowych. W związku z tym w zakresie obowiązków pracowników było również dostarczanie pustych palet do ww. stanowisk.
Funkcjonowanie przedsiębiorstwa po automatyzacji
Przewożoną jednostką logistyczną jest ustandaryzowana paleta EPAL. Standardowy ładunek umieszczony na palecie to kilka lub kilkanaście rolek etykiet produkowanych przez klienta o łącznej masie do 500kg. Operatorzy maszyn po zapełnieniu palety lub zakończeniu zlecenia, za pomocą panelu operatora, wywołują żądanie transportu. To działanie generuje misję transportową dla robota AGV. Docelowy punkt logistyczny pobierany jest z systemu zarządzania produkcją. Po przewiezieniu palety z ładunkiem robot wraca na stanowisko z pustą paletą pod następne zlecenie.
Infrastruktura
W zaprojektowanym systemie zautomatyzowanego transportu inżynierowie wykorzystali robota IntraBot Lift 550, którego udźwig wynosi 550 kg, a jego konstrukcja pozwala na obrót w miejscu. Ma to ogromne znaczenie podczas wjazdu do doków. W celu umożliwienia poboru i odłożenia palet z punktów logistycznych zamontowano 6 doków odkładczych. Na hali zamontowano tablicę synoptyczną pokazującą miejsce, w którym znajduje się robot AGV. Doki docelowe wyposażone są w sygnalizatory świetlne informujące pracowników działu magazynowego o konieczności odbioru palety z doku.
Dostosowanie możliwości systemu intralogistycznego do potrzeb klienta
Choć roboty mobilne producenta Etisoft Smart Solutions Sp. z.o.o pozwalają na autonomiczną jazdę (AMR) to aby zwiększyć niezawodność i precyzję jazdy, na potrzeby tego zakładu, robot porusza się po wydzielonych ścieżkach na zamontowanych taśmach magnetycznych (AGV). Zwiększa tym samym bezpieczeństwo pracowników mogących przewidzieć tor ruchu pojazdu. Dodatkową korzyścią ze wdrożenia systemu jest poprawa porządku w obrębie ścieżek transportowych.
Drugim aspektem bezpieczeństwa było ograniczenie prędkości robota w zależności od strefy. Robot potrafi osiągnąć prędkość 5 km/h. Aby zapewnić pełne bezpieczeństwo pracownikom na hali, robot porusza się z prędkością do 2 km/h. Zwalnia do 1 km/h, gdy w obrębie strefy ostrzegawczej znajdują się ludzie lub przedmioty. Zatrzymuje się gdy narusza strefę ochronna. Wszystko służy zachowaniu bezpieczeństwa pracowników oraz bezpieczeństwa przewożonego ładunku.
Za sukcesem wdrożenia kryją się ludzie
Wdrożony system intralogistyczny dowodzi możliwości automatyzacji procesów w istniejących halach z zachowaniem pełni bezpieczeństwa dla ludzi i ładunków. Trzeba mieć jednak na uwadze, że istotnym czynnikiem wpływającym na powodzenie projektu w tym przypadku była i jest dyscyplina pracowników, otwartość na innowacje i zaangażowanie kadry zarządzającej.