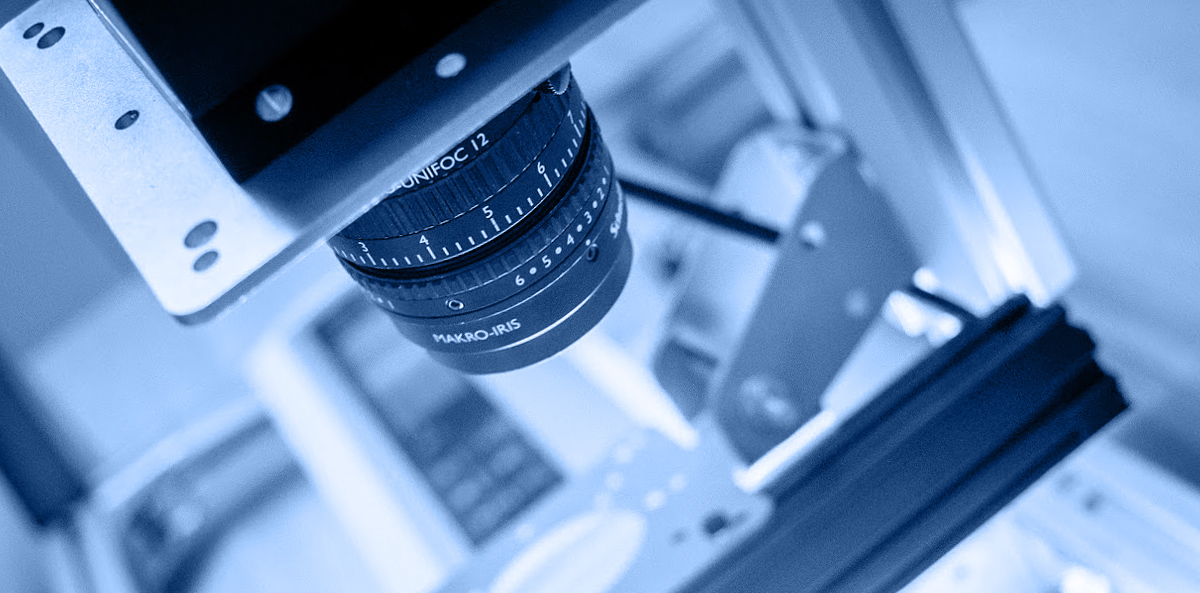
Automatyczna kontrola jakości przy pomocy systemu wizyjnego w 6 krokach – cz. I
Aby utrzymać się w konkurencyjnym środowisku firmy coraz częściej drobiazgowo śledzą i kontrolują wszystkie elementy procesu produkcji wykorzystując rozwiązania typu Machine Vision. Dzieje się tak nie tylko ze względu na dążenie do optymalizacji procesów pod kątem wydajności i kosztów. Również ze względu na konieczność spełnienia coraz ostrzejszych wymagań prawnych. Jak się do tego ma automatyczna kontrola jakości?
Przedsiębiorcy zdają sobie sprawę, że mogą włożyć wiele wysiłku i przeznaczać duże nakłady na promowanie marki, zdobywanie zamówień oraz ich wydajną realizację. Jeśli jednak jakość produktów końcowych będzie niska lub zmienna to zadowolenie klientów, a tym samym liczba kontraktów i przychodów, zaczną topnieć.
Ze względu na złożoność procesów produkcyjnych i logistycznych, systemy wizyjne kontroli jakości dostosowuje się do określonych wymagań. Zarówno pod względem rodzaju przeprowadzanych kontroli, jak i przepustowości systemu. Może to stanowić wyzwanie dla zakładów produkcyjnych szukających rozwiązań na własną rękę.
Poniżej przedstawiamy pierwszą część artykułu jak w 6 krokach wdrożyć system automatycznej weryfikacji wizyjnej z perspektywy integratora.
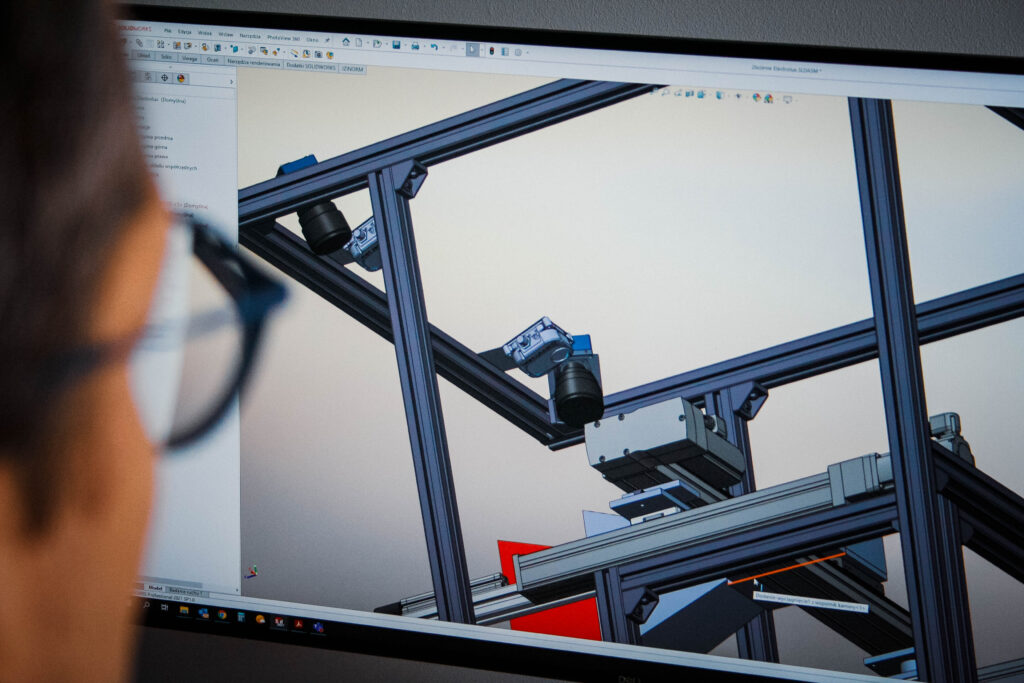
Automatyczna kontrola jakości, a analiza potrzeb klienta
Aby wizyjny system kontroli jakości był w stanie we właściwy sposób rozwiązać problemy, niezbędne jest jasne określenie celów biznesowych. Także – potrzeb klienta, jakie może zaspokoić implementowany system. Celem może być, na przykład, zmniejszenie liczby wadliwych produktów opuszczających zakład przemysłowy. Może to być także rejestracja wyników kontroli gotowych produktów, śledzenie procesu produkcji wyrobu medycznego. Również – wydajniejszy proces wysyłki gotowych wyrobów lub cyfryzacja i automatyzacja produkcji. Inną ważną kwestią jest dostosowanie inwestycji do zaplanowanego budżetu na bieżące lub strategiczne działalności zakładu.
Na tym etapie konsultacja z integratorem jest bardzo dużym wsparciem. To eksperci potrafią przełożyć potrzebę klienta na konkretne założenia funkcjonalne systemu i przewidzieć ewentualne wyzwania. Zebrane informacje są podstawą do przygotowania wstępnej koncepcji rozwiązania.
Kolejne kroki analizy biznesowej
- Analiza przedwdrożeniowa
Krok ten jest naturalną konsekwencją analizy celów biznesowych i procesu produkcji. Polega na wykorzystaniu danych zgromadzonych w arkuszach, szablonach i informacji uzyskanych w trakcie konsultacji. Pomagają one określić czy zaproponowany wizyjny system kontroli jakości będzie spełniał założenia funkcjonalne projektu oraz pozwoli osiągnąć wyznaczone cele biznesowe.
Jeśli celem projektu jest zmniejszenie liczby wadliwych części opuszczających zakład to skuteczność rozwiązania można określić na podstawie liczby części identyfikowanych przez system wizyjny jako niezgodnych z wzorcem. W przypadku wyrobu medycznego może być zapewnienie traceability w procesie produkcyjnym. Chodzi o dokładną identyfikację miejsca wystąpienia zgodności lub niezgodności w oparciu o zarejestrowane zdjęcia z procesu kontroli jakości.
Na tym etapie wyznacza się cele dla PoC (Proof of Concept). Pozwalają one określić, czy przyjęty model rozwiązania odpowiada na wszystkie wymagania klienta. Przeprowadza się także uproszczoną symulację rzeczywistego procesu. Określa się wstępne algorytmy wizyjne, a także ryzyko projektowe oraz czas realizacji i budżet projektu. Przygotowywana jest też wizualizacja samego stanowiska wizyjnego systemu kontroli jakości.
- Uzasadnienie biznesowe
Etap ten pozwala określić korzyści biznesowe wynikające z rozwiązania, takie jak:
- przychody, które można uzyskać. Na przykład:
- możliwość oferowania klientom nowych usług, takich jak informacje i raporty dotyczące każdego wyprodukowanego wyrobu
- wsparcie w przypadku wykrycia wad wyrobu i szukania problemu w całym łańcuchu dostaw i produkcji
- korzyści wynikające z dobrej współpracy z klientami, którzy cenią terminowe dostawy niezawodnych produktów.
- koszty, których można uniknąć. Na przykład:
- pracy kontrolerów manualnych
- wynikające bezpośrednio z pomyłek ludzkich, takie jak koszty wycofania lub naprawy wadliwych wyrobów wysłanych do klientów
- odbudowania utraconej renomy firmy.
W przypadku wdrożenia systemu wizyjnego w Lumileds Poland projekt pozwolił zmniejszyć liczbę przestojów. Także wyeliminować błędy pakowania i zmniejszyć straty wynikające z uszkodzeń produktów i reklamacji. Zapewnił także poprawne pakowanie produktów oraz wyeliminował konieczność nadzoru procesu przez pracownika.
Jeżeli artykuł Cię zainteresował i szukasz systemu wizyjnego do automatycznej kontroli jakości to…