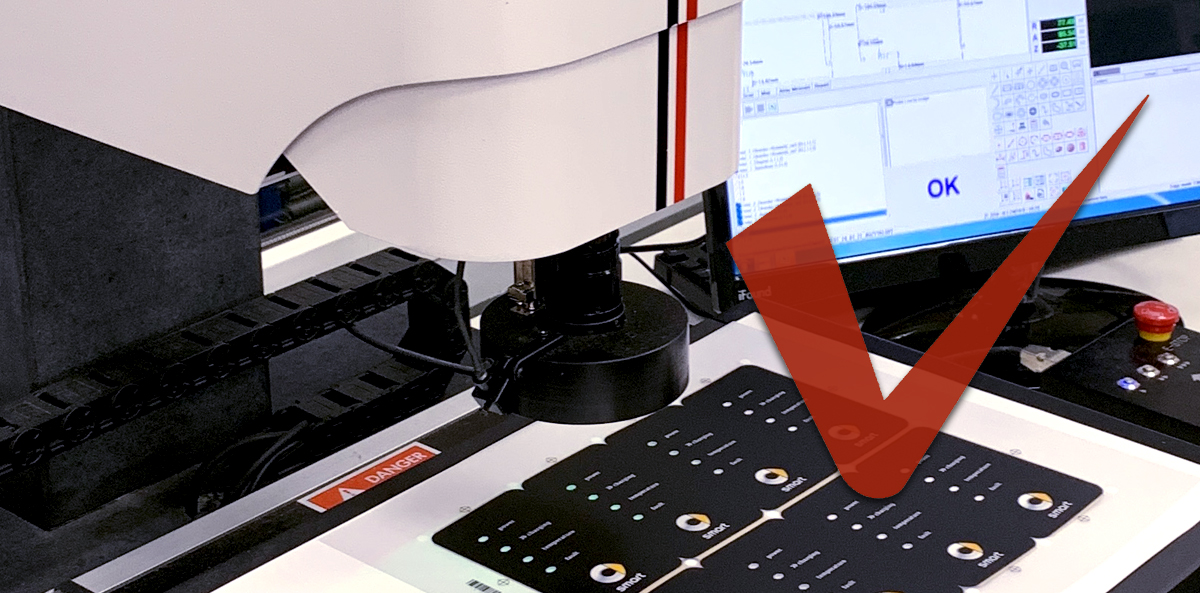
Panele czołowe i kontrolne: pomiary i kontrola jakości podczas produkcji
Coraz bardziej sprecyzowane oczekiwania klientów, a także w obliczu rosnącej konkurencji, przedsiębiorstwa poligraficzne stają w obliczu wielu wyzwań. Jednym z najważniejszych jest spełnienie oczekiwań jakościowych zgodnych z wymaganiami i specyfikacjami odbiorcy oraz przyjętymi normami dla danej grupy produktów. Jednocześnie towarzyszy im optymalizacja kosztów produkcji. Panele czołowe i kontrolne – jak przebiega u nas kontrola jakości podczas całego procesu?
Odpowiednio zautomatyzowana kontrola jakości na poszczególnych etapach produkcyjnych jest dziś niezbędnym narzędziem. Stosuje się ją w celu monitorowania zgodności produkowanych wyrobów z przyjętymi standardami, w oparciu o ściśle określone procedury. Pozwala ona wykryć wady oraz obszary ich występowania na wczesnych etapach produkcji. W przypadku wszelkiego rodzaju paneli czołowych, ozdobnych czy kontrolnych ma to ogromne znaczenie. Dlatego też restrykcyjna kontrola jakości na każdym etapie produkcji oraz kontrola wyrobu gotowego jest szczególnie istotna. Pozwala uniknąć nie tylko późniejszych reklamacji, ale przede wszystkim na:
- szybkie wykrycie wad
- rozpoznanie obszaru ich powstawania
- wprowadzenie działań korygujących.
Na podstawie zapisów z takich działań możliwa są analizy, które wpłyną na eliminację zidentyfikowanych problemów oraz poprawę jakości i wydajności. Tym samym na redukcję strat i odpadów. Z punktu widzenia odbiorcy jest to także bardzo istotne. Daje mu bowiem pewność otrzymania produktu zgodnego z jego oczekiwaniami. Bez szczegółowej kontroli wejściowej może go użyć w swojej dalszej produkcji.
Panele czołowe i kontrolne: weryfikacja jakości na każdym etapie produkcji
Za kontrolę jakości przyjmuje się wszelkie zautomatyzowane i ręczne czynności kontrolne. Są one wykonywane według ściśle określonych procedur i wytycznych na wszystkich etapach produkcji, aż po wyrób gotowy.
W naszej firmie, w oparciu o procedury ISO 9001 i 14001 stosowane są różne procesy kontrolne i pomiarowe, zależnie od rodzaju samego produktu. W wielu przypadkach wdrażamy działania kontrolne przygotowane specjalnie w oparciu o wymogi odbiorcy jak np. pomiary rezystancji zadrukowanego obszaru.
Do podstawowych czynności kontrolnych należą:
- Weryfikacja i kontrola materiału wejściowego na którym realizowany ma być nadruk. Najczęściej są to arkusze tworzywa sztucznego lub gotowe komponenty pochodzące z wtryskarki. Weryfikacja ta poza sprawdzeniem specyfikacji materiałowej surowca i spełnienia norm RoHS, polega na sprawdzeniu wymiarów oraz ogólnej oceny wizualnej pod kątem wad takich jak zarysowania, zagniecenia, zanieczyszczenie, zapylenie itp. Po kontroli na magazynie wejściowym materiał jest odpowiednio oznakowany i zwolniony do produkcji.
- Weryfikacja i kontrola pozostałych materiałów użytych na poszczególnych etapach produkcji. Kontrola dotyczy wydania do produkcji warstw klejowych oraz farb sitodrukowych specjalnie oznakowanych i przypisanych w systemie do konkretnego produktu i zlecenia. Farby przed wydaniem do produkcji sprawdzane są pod kątem daty ich przydatności oraz właściwej konsystencji i zgodności koloru z wzorcem. Oznakowanie farby pozwala na eliminacje ryzyka pomyłki i użycia przez operatora niewłaściwej farby do danego produktu. Specjalny system nadzoru produkcji z terminalem i skanerem przy każdym gnieździe produkcyjnym sprawdza poprawność użytego w procesie materiału czy farby.
- Kontrola i zwolnienie druku. Pierwszym etapem produkcji jest przygotowanie i uzbrojenie maszyny drukującej pod realizację konkretnego produktu. Następnie zalanie odpowiednimi farbami i ustawienie zapisanych wcześniej parametrów druku dla danego produktu. Na tym etapie wykonuje się pierwsze zadruki i korekty ustawień, aż do uzyskania pierwszej tzw. dobrej sztuki. Trafia ona do kontrolera jakości. Sprawdza on jej zgodność ze zarchiwizowanym wzorcem zatwierdzonym przez klienta oraz dostępną w systemie specyfikacją wymiarową i dokumentacją techniczną.
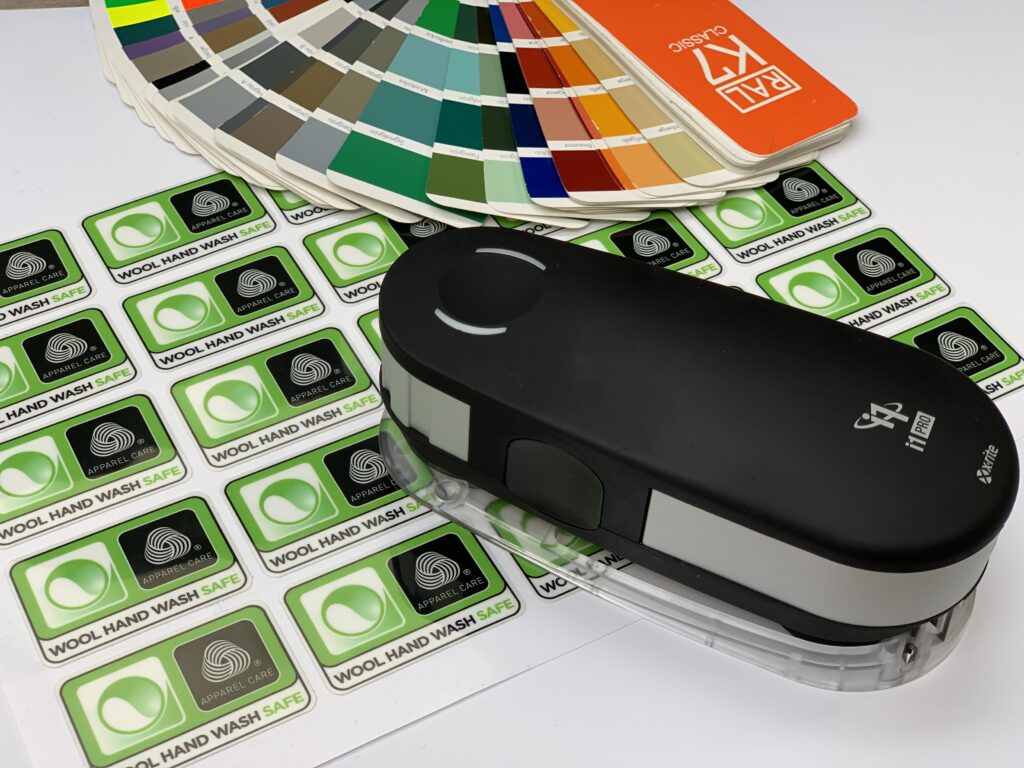
Jak odbywa się kontrola procesu?
- wizualne porównanie z fizycznym wzorcem pochodzącym z produkcji samplowej lub z wzorcem otrzymanym od klienta oraz sprawdzenie zgodności graficznej z obrazem podpiętym do karty produktu w systemie informatycznym
- sprawdzenie intensywności i poprawności koloru z użyciem spektrofotometru
- sprawdzenie głównych wymiarów i pozycji nadruku na arkuszu lub gotowym produkcie za pomocą zautomatyzowanego systemu pomiaru wizyjnego
- wykonanie testów trwałości nadruku i przyczepności farby do podłoża: (test siatki nacięć, test ścierania, test odporności na czynniki chemiczne)
- inne testy specjalne wskazane przez odbiorcę.
Teraz następuje zwolnienie druku do produkcji seryjnej lub jej zablokowanie.
Czas na poprawki
- Kontrola w trakcie druku. Konstrukcja maszyn sitodrukowych oraz sam proces druku dają bardzo ograniczone możliwości instalacji zautomatyzowanych systemów wizyjnej kontroli jakości działających in-line w samej maszynie. W praktyce stosuje się zatem kontrolę wizyjną zewnętrzną po wyjściu z maszyny. Wówczas pracownik kontroli jakości lub sam operator dokonuje wizualnej oceny 100% wychodzących produktów lub arkuszy. Sprawdza poprawność nadruku i wyłapuje ewentualne wady lub odchyłki od normy. Wadliwe produkty i półprodukty znakuje się i odkłada do osobnego pojemnika. W zależności od przypisanej do danego produktu procedury, w trakcie druku dokonujemy bardziej szczegółowej weryfikacji poprawności i pozycji nadruku za pomocą cyfrowych urządzeń pomiarowych. Umożliwiają one operatorowi korygowanie ewentualnych odchyłek lub eliminacje wad.
- Kontrola międzyoperacyjna. Produkcja wszelkiego rodzaju paneli: drukowanych bezpośrednio na gotowych elementach, jak i tych na arkuszach, składa się z wielu procesów. Na każdym z tych etapów występują określone procedury kontrolne. Używamy wówczas urządzeń pomiarowych, wizyjnych systemów pomiarowych oraz gotowych przymiarów otrzymanych od odbiorcy.
- Znakowanie produktu. Każdy pojedynczy wyrób gotowy na końcowym etapie produkcji znakuje się niewielką, spersonalizowaną naklejką z kodem QR. Pozwala ona na pełną identyfikację produktu oraz sprawdzenie jego całej ścieżki produkcyjnej. Od wydania surowca i materiałów dodatkowych po wyrób finalny. Dzięki temu w łatwy sposób można określić z jakiej partii lub jakiej dostawy pochodzi dany produkt. W przypadku ewentualnej reklamacji jest to bardzo istotne. Dzięki temu można podjąć konkretne i ukierunkowane działania naprawcze.
- Kontrola końcowa. Pomimo wielu etapów kontrolnych w czasie produkcji oraz przy pakowaniu wyrobu gotowego, wszystkie produkty trafiają do magazynu pośredniego. Działa on pod nadzorem działu Kontroli Jakości. Pracownik tego działu dokonuje pełnej kontroli losowo wybranych produktów. Od poprawności graficznej, poprzez dokonanie pomiarów, sprawdzenie kolorystyki, aż po sposób pakowania i zgodność ilościową. Po odpowiednim oznakowaniu opakowań zbiorczych produkty (panele czołowe i kontrolne oraz inne produkowane przez nas) przekazujemy na główny magazyn wysyłkowy.
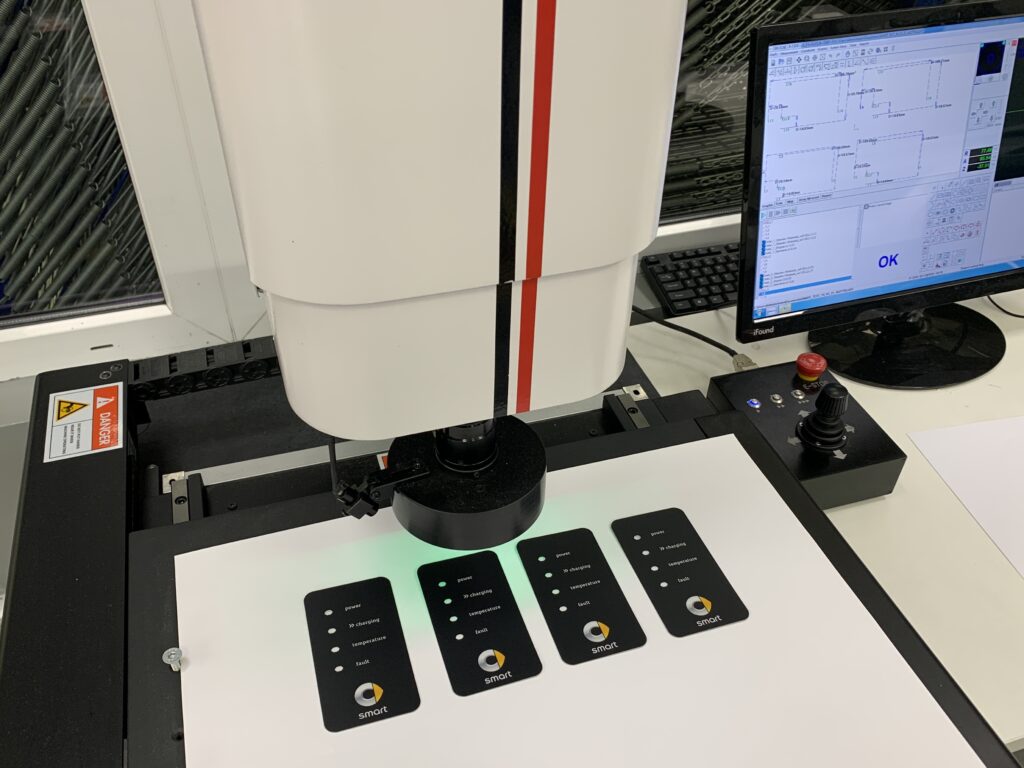
Powtarzalność w procesie produkcji paneli
Opisane w dużym skrócie procesy i etapy kontrolne mają na celu zapewnić bezpieczeństwo łańcucha dostaw. Chodzi także o gwarancję doskonałej i powtarzalnej jakości oraz 100% zgodności z wymaganiami klienta. Jednocześnie chronią, nie tylko nas jako dostawcę komponentów, ale przede wszystkim odbiorcę od konsekwencji dostarczenia wadliwego produktu końcowego na rynek. Kontrola jakości ma także zasadnicze znaczenie dla poprawy procesów produkcyjnych. Jednocześnie przyczynia się do wzrostu świadomości i odpowiedzialności wśród pracowników. Umożliwia bardziej efektywne wykorzystanie zasobów i otrzymanie przy tym produktów o wysokiej i sprawdzonej jakości przy obniżonych kosztach. produkcji.
Mając na uwadze powyższe korzyści, nieustannie doskonalimy procedury kontrolne oraz inwestujemy w nowoczesne urządzenia i systemy kontroli jakości.
Jeśli więc produkujesz urządzenia wymagające montażu paneli – skontaktuj się z nami. Panele czołowe i kontrolne produkujemy od wielu lat. Na rynek wprowadziliśmy już ponad 100 mln sztuk paneli frontowych różnego typu.